Comprehensive Guide to Basket Strainers: Design, Applications, and Maintenance
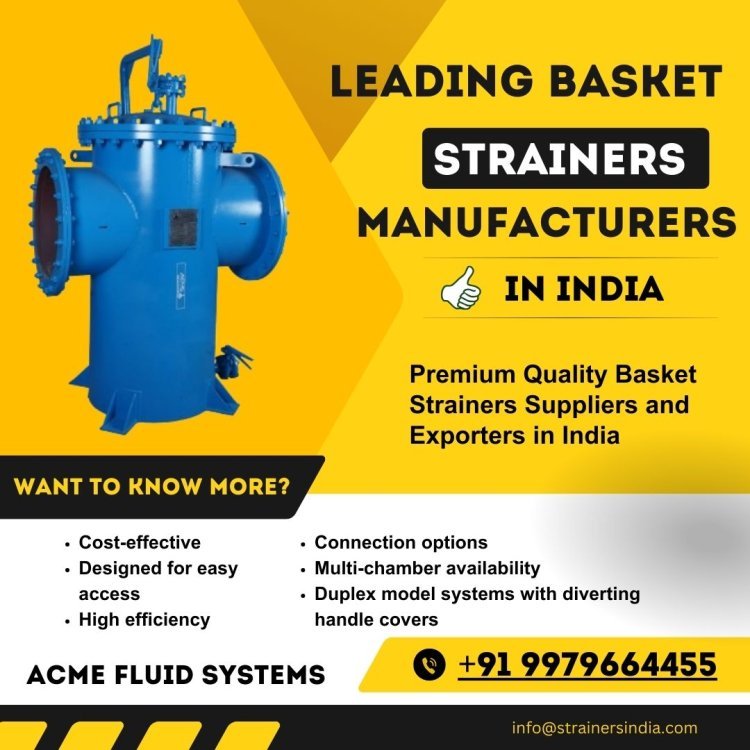
In industrial fluid systems, maintaining the purity of process streams is paramount. Basket strainers serve as essential components, effectively removing unwanted solids and debris from pipelines, thereby safeguarding equipment and ensuring optimal operational efficiency.
Understanding Basket Strainers
Basket strainers are devices installed in pipelines to filter out foreign particles from fluids. They feature a perforated or mesh-lined basket that captures debris while allowing clean fluid to pass through. The design facilitates easy removal and cleaning of the collected solids, making them indispensable in various industrial applications.
Key Features of Basket Strainers
- High Debris Holding Capacity: Basket strainers are designed to accommodate substantial amounts of debris without frequent maintenance interruptions.
- Low Pressure Drop: Engineered to minimize resistance to fluid flow, ensuring system efficiency.
- Versatility in Design: Available in various materials such as carbon steel, stainless steel, and cast iron, catering to diverse industrial requirements.
- Ease of Maintenance: The removable basket allows for straightforward cleaning and reinstallation, reducing downtime.
Applications of Basket Strainers
Basket strainers are utilized across multiple industries to protect equipment and maintain process integrity. Notable applications include:
- Pharmaceutical Industry: Ensuring the purity of liquid pharmaceuticals by removing contaminants.
- Food and Beverage Production: Filtering out impurities to comply with health and safety standards.
- Power Generation: Protecting turbines and pumps from particulate damage.
- Water Treatment Facilities: Removing debris from water sources to prevent equipment fouling.
- Automotive Manufacturing: Filtering fluids in production lines to maintain product quality.
Types of Basket Strainers
Understanding the different configurations of basket strainers aids in selecting the appropriate type for specific applications.
Simplex Basket Strainers
- Design: Consist of a single basket chamber.
- Operation: Require system shutdown for cleaning, suitable for processes where temporary interruption is acceptable.
Duplex Basket Strainers
- Design: Feature dual basket chambers with a flow-diversion mechanism.
- Operation: Allow continuous operation by diverting flow to one chamber while the other is serviced, eliminating downtime.
Fabricated Basket Strainers
- Design: Custom-built to meet specific system requirements.
- Operation: Offer flexibility in size, material, and pressure ratings, tailored to unique industrial applications.
Maintenance and Best Practices
Proper maintenance of basket strainers is crucial for sustained performance and longevity.
Routine Inspection and Cleaning
- Scheduled Checks: Regularly inspect strainers for debris accumulation.
- Cleaning Procedure: Depressurize the system before removing the basket. Clean the basket using appropriate solvents and brushes to remove all trapped particles.
Monitoring Pressure Drop
- Installation of Gauges: Place pressure gauges upstream and downstream of the strainer to monitor differential pressure.
- Interpreting Readings: A significant increase in pressure drop indicates clogging, signaling the need for cleaning.
Replacement and Spare Parts
- Spare Baskets: Keep replacement baskets on hand to facilitate quick swaps during maintenance.
- Seal Integrity: Regularly inspect and replace seals and gaskets to prevent leaks.
Conclusion
Basket strainers are vital components in industrial fluid systems, offering efficient filtration to protect equipment and maintain process quality. By selecting the appropriate type and adhering to regular maintenance practices, industries can ensure the longevity and effectiveness of their fluid handling systems.
What's Your Reaction?






